This article is an installment of Future Explored, a weekly guide to world-changing technology. You can get stories like this one straight to your inbox every Thursday morning by subscribing here.
The world’s biggest 3D-printed housing project is now underway.
Over the next 5 years, 3D printing construction company Alquist 3D plans to build 200 houses in rural parts of Virginia. If this undertaking — “Project Virginia” — is a success, it’ll be the best evidence yet that 3D printing could help solve America’s affordable housing crisis.
Why it matters
Owning a home is one of the best ways to improve your economic standing in the US, as it allows you to build equity and improve your credit score.
Mortgage payments are often lower and more stable than rent, which is at an all-time high, and homeowners get tax deductions that aren’t available to renters. That makes it easier to plan and save for other major financial investments, such as retirement or college funds.
“[Buying a home is] a sign of arrival…It has meant a huge deal for this country.”
Anthony Alofsin
Rental housing vacancies are at an all-time low, meaning it can be hard to even find a rental — owning can deliver the peace of mind that comes with stable housing, plus it’s simply nice to be able to remodel and decorate your home however you want.
“[Buying a home is] a sign of arrival. It’s a sign of psychological and emotional security,” architect Anthony Alofsin told NPR. “It has meant a huge deal for this country.”
The challenge
Right now, it’s incredibly difficult to transition from renter to homeowner.
That’s partly because average home prices are at an-all time high, but a bigger issue is a shortage of houses — according to a report by mortgage financier Freddie Mac, at the end of 2020, the US was 3.8 million homes short of where it needed to be to meet demand.
An estimate through June 2021 from Realtor.com put the shortage at over 5 million homes to keep up with the rate of new household formation.
We’re not just short of homes in general, but also particular kinds of houses: the kind that new homebuyers can afford.
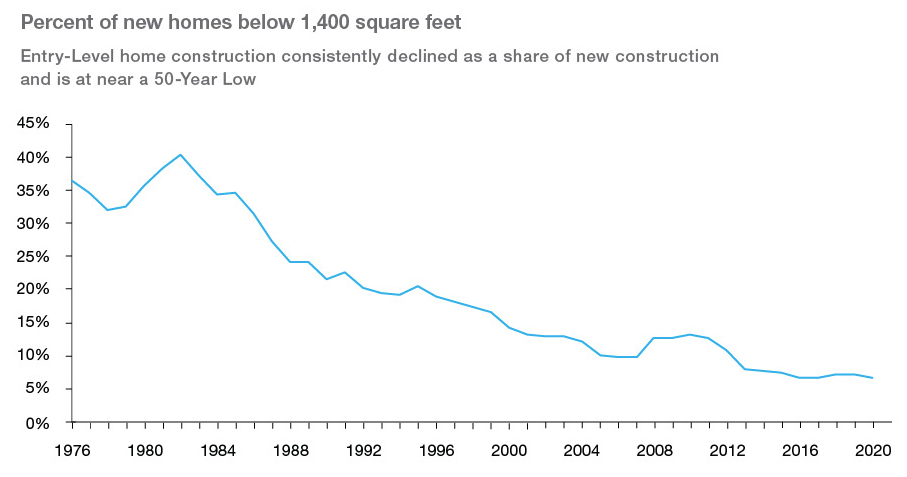
The biggest driver, according to Freddie Mac, is the huge decline in the construction of entry-level homes — single-family houses under 1,400 square feet. In the early-1980s, they accounted for 40% of newly constructed houses, but by 2019, the rate had dropped to 7%.
“Simply put, we must build more single-family entry-level housing to address this shortage, which has strong implications for the wealth, health, and stability of American communities,” wrote the company.
A multitude of factors are contributing to this construction decline, but two major ones mentioned in Freddie Mac’s report are an ongoing labor shortage and rising material costs.
3D printing could help the industry overcome both.
3D printing houses
At its core, the process of 3D printing houses is the same as 3D printing anything else.
First, a model of the object is created in a computer program. A 3D printer then extrudes a liquid building material from its nozzle to build the object from the ground up, adding layer on top of layer, sometimes with pauses for the material to dry, until construction is complete.
The difference is that, with desktop 3D printers, the building material is usually a type of plastic, and the surface is a small glass plate. When 3D printing houses, the building material is typically concrete, and the surface is a house-sized plot of land.
The printer needs to be massive to build something as large as a house — for Project Virginia, Alquist will use Black Buffalo 3D’s NEXCON printer, which weighs 19 tons and can print structures up to 3 stories high, thanks to its gantry and track system.
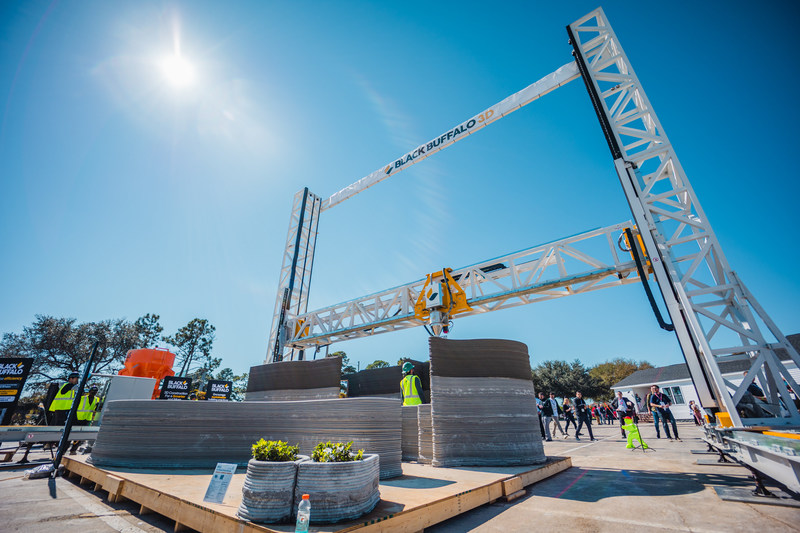
In December 2021, Alquist worked with Habitat for Humanity to build the organization’s first 3D-printed home.
That build took just 28 hours, cutting 4 weeks off the schedule and reducing building costs by 15% per square foot. The savings were mainly due to the need for fewer workers and less lumber, which is both more expensive and harder to source than it used to be.
Alquist is now following up that build with Project Virginia, a plan to construct 200 similar homes in Virginia.
At least four different designs will be utilized for the project, and each finished home will cost $175,000 to $350,000, according to Alquist.
The goal is to have several houses built by the end of 2022 and all 200 constructed within four or five years — that should give the group enough time to identify building sites, 3D print the exteriors, and complete all the other work that goes into constructing a house.
“There’s nothing different about one of our homes versus any other home except that the exterior walls are made out of concrete instead of wood,” Alquist CEO Zachary Mannheimer told TIME.
“These homes are built nearly identically otherwise,” he continued. “Our process just involves extruding concrete from a giant robot, which gives you savings in time and labor and material.”
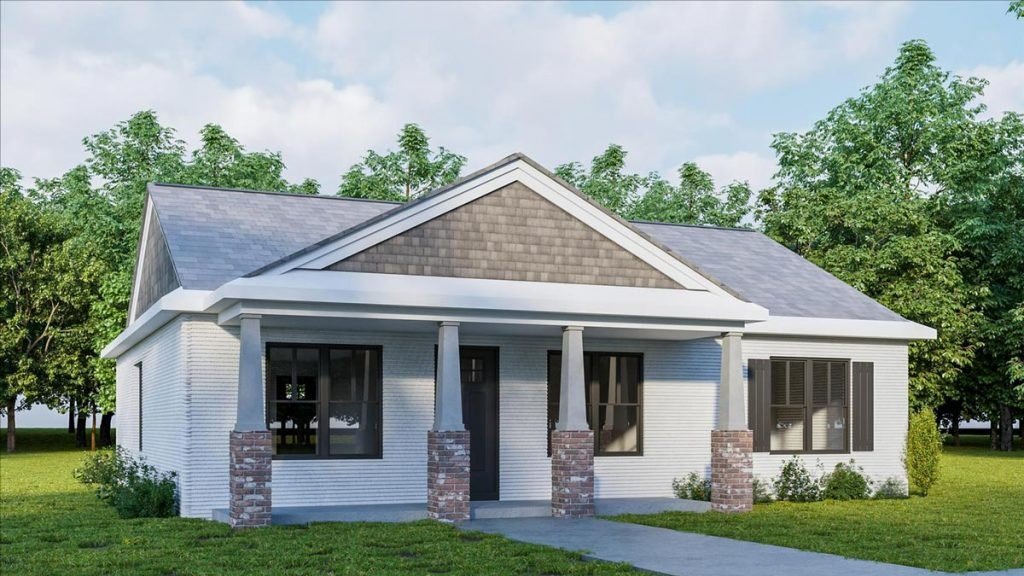
Project Virginia kicked off on April 29 with a demonstration of the NEXCON printer in Pulaski, Virginia, where Alquist will start building the initiative’s first house — a single-story, 1,280-square-foot home with 3 bedrooms and 2 bathrooms — in the summer of 2022.
Pulaski and Roanoke were chosen as the first two cities in Project Virginia due to a recent increase in housing demand spurred by Volvo, Blue Star Manufacturing, and American Glove Innovations bringing 3,000 new jobs to the area.
“With migration patterns shifting due to pandemic, climate, and economic concerns, smaller communities like Pulaski have a huge need — and an amazing opportunity — to develop affordable housing for new residents,” said Mannheimer.
The big picture
By 3D printing houses, companies like Alquist may help address the shortage of affordable homes in the US, but the approach won’t solve the problem by itself, at least not in the near future, and not without dramatically scaling up.
One issue is that there simply aren’t enough companies to meet the demand, and they aren’t big enough. Alquist alone has been averaging 20 to 50 requests for new homes every hour since they announced their build with Habitat for Humanity, Mannheimer told TIME.
“At the moment, there’s less than 10 companies using this technology in America,” he said. “To really make a dent in the affordable housing crisis, we’d need more like 50.”
Many builders run into issues with appraisers, regulators, and other officials when planning 3D printing projects.
Because land is at a premium in major cities, which have the most severe housing shortage, it would make more sense for new construction to be taller, multi-unit structures — something that 3D printers can’t do yet. So for now, the tech is best suited to rural or suburban homes.
3D printing also speeds the construction of a home’s frame, but that’s just one part of the process — the technology can’t address labor and material shortages involving electrical systems, plumbing, windows, appliances, and more.
There are also external hurdles. 3D-printed houses may be functionally identical to their traditional counterparts, but they do look different and are still a novelty, so many builders run into issues with appraisers, regulators, and other officials when planning projects.
“We can have zoning officials who can just say, ‘We don’t like the look of it,’” Andrew McCoy, a professor at the Virginia Center for Housing Research, who helped build the Habitat for Humanity house, told Housing Wire. “They can find things to nitpick on.”
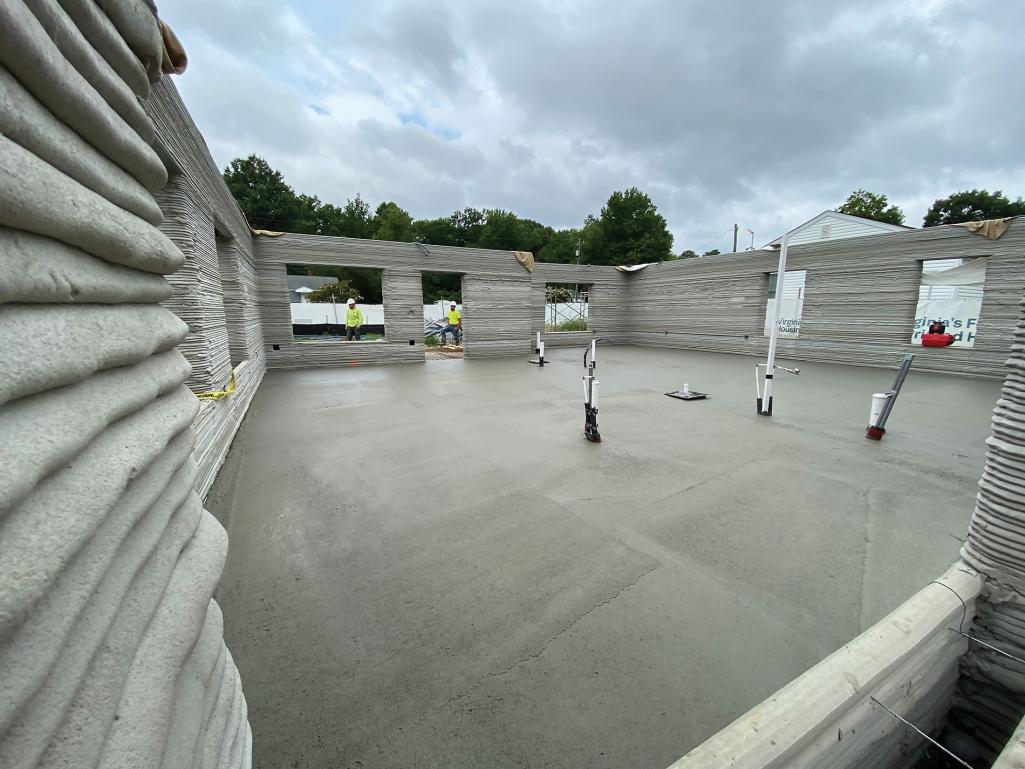
Ultimately, Mannheimer is confident that 3D printing will be able to overcome existing hurdles to become the future of construction.
He recently told Business Insider he expects you’ll find a 3D printer on every commercial and residential site before Project Virginia wraps up, and by 2027, he thinks 3D printing houses will be more common than building them the old-fashioned way.
The success of Project Virginia could play a major role in bringing the vision of the future to fruition, and Alquist has the benefit of government backing for the project — the town of Pulaski actually contacted the company about 3D printing houses in the city and not the other way around.
“We have been down for a long time, and now is our time,” Pulaski Mayor Shannon Collins said of Project Virginia. “We are coming into the 21st century with this, and we’re coming in hot.”
We’d love to hear from you! If you have a comment about this article or if you have a tip for a future Freethink story, please email us at tips@freethink.com.